In semiconductor manufacturing, it is said that the majority of defects are caused by particles adhering to the products. To reduce the number of defective products, a clean environment is indispensable, and cleanrooms play a crucial role in creating this environment. Cleanrooms are designed to strictly control fine dust and chemical substances in the air to protect product quality. This article explains cleanrooms installed in semiconductor factories, including their mechanisms, the necessity in semiconductor manufacturing, and the performance requirements for cleanrooms in these factories.
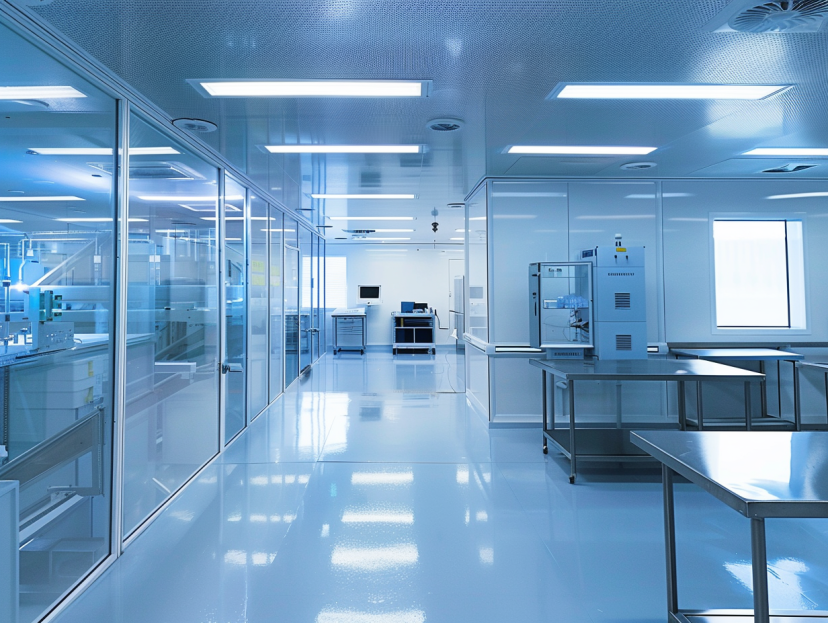
1. What is a Cleanroom in a Semiconductor Factory and Why is it Necessary?
A cleanroom is a room where air cleanliness is strictly controlled to maintain the amount of airborne dust and debris below a certain level. Semiconductors, being precision equipment, suffer quality degradation and defect occurrence if foreign substances mix during the manufacturing process. By working in a cleanroom where air cleanliness is managed, contamination is prevented, and product quality is maintained. The foreign substances referred to here include not only dust and debris but also microscopic particles and microorganisms invisible to the naked eye.
In addition to dust and microorganisms, semiconductor factories must also be cautious of fiber lint and metal fragments. Cleanrooms used to prevent quality degradation of products are also commonly utilized in factories producing precision equipment, electronics, food, and medical products. The required cleanliness level varies depending on the industry and product, and parameters such as humidity, temperature, and pressure are controlled as needed.
2. Mechanisms of Cleanrooms in Semiconductor Factories
To explain the mechanisms that maintain cleanliness in cleanrooms simply, there are two key points:
- Purification of incoming air using ultra-high-performance filters to prevent foreign substances from entering.
- Elimination of foreign substances through air circulation within the room.
Cleanrooms are constructed with walls, raised floors, and ceilings made of specialized partitions called cleanroom partitions. There are two main types of air circulation methods: “vertical unidirectional flow” and “turbulent flow (non-unidirectional flow).” Let’s explain each:
1) Vertical Unidirectional Flow Method
This method involves installing fans at the top of the cleanroom to blow clean air in a downward direction towards the floor. It is also known as the downflow method. Due to its high purification effect, this method is mainly adopted in semiconductor factories. However, it has high initial and running costs and is challenging to expand once installed.
2) Turbulent Flow (Non-Unidirectional Flow) Method
In this method, exhaust ports are installed on part of the walls to push the air outside while circulating it to dilute and maintain the cleanliness of the particulate matter in the room. It is also called the conventional method. Compared to the vertical unidirectional flow method, its cleanliness is inferior, but it has the advantage of lower initial and running costs.
3. Required Cleanroom Class for Semiconductor Factories
Cleanroom cleanliness is categorized based on the amount of impurities in the air. The cleanliness level is referred to as “class,” determined by the number of impurities per unit volume. Although transitioning to international unified standards set by ISO, the semiconductor industry often uses the older U.S. federal standards.
Currently, cleanroom standards are defined by ISO, categorized into nine levels: ISO Class 1 to Class 9. Under older standards, terms like Class 100, 1000, and 10,000 were used. The U.S. federal standards classify cleanrooms based on the number of particles 0.5μm or larger per cubic foot of air. For instance, a cleanroom with fewer than 1,000 particles of 0.5μm or larger per cubic foot is Class 1000, and fewer than 100 particles is Class 100. The smaller the number following the class, the higher the cleanliness of the room.
Cleanroom Classes for Semiconductor Manufacturing
Due to the high cleanliness required for semiconductor manufacturing, cleanrooms installed in semiconductor factories are typically Class 1 to 100.
- Generally, high-level cleanliness is required in semiconductor factories, corresponding to ISO 14644-1 standards Class 3 to 5 (U.S. federal standards Class 1 to 100) for manufacturing.
- Semiconductor manufacturing equipment, components, precision machinery, and electronic parts are manufactured in cleanrooms corresponding to ISO 14644-1 standards Class 5 to 7 (U.S. federal standards Class 100 to 10,000).
4. Cleanroom Design Requirements for Semiconductor Manufacturing Processes
This section explains key points for constructing clean environments (cleanrooms) to improve yield and prevent contamination in semiconductor manufacturing processes. Constructing high cleanliness class and energy-efficient cleanrooms (sustainable for long-term operation):
1) Selecting the Cleanliness Class
Select the optimal cleanliness class. Adopt the laminar flow method to optimize air circulation, realizing high cleanliness through optimal airflow methods that prevent contaminant stagnation. Choose appropriate ventilation rates and filters (HEPA filters, ULPA filters) to maintain cleanliness. Additionally, design an HVAC system capable of controlling temperature and humidity. Use anti-static clean panels to suppress dust generation, characterized by smooth, gap-free walls and ceilings that are easy to clean.
2) Temperature and Humidity Control
Select high-precision sensors to accurately measure temperature and humidity and install them in appropriate locations. Implement a centralized management system that allows remote monitoring of temperature and humidity data in real time. Design HVAC systems and humidification/dehumidification devices to achieve stable environmental conditions. Construct a system capable of responding quickly to minimize the impact of external environmental changes.
3) Energy-Efficient Cleanrooms
Select high-efficiency HVAC systems and energy-efficient equipment like LED lighting. Optimize air conditioning systems according to the cleanliness class. Implement local environmental construction based on usage to achieve energy savings. Enhance the thermal insulation performance of the building structure itself by using high-insulation clean panels to reduce the impact of external heat. Adopt energy-saving systems that can adjust the output of air conditioning and lighting according to the usage environment. Design flexible layouts to easily accommodate future technological advancements or changes in usage.
Achieving and maintaining a high level of cleanliness in semiconductor manufacturing is paramount to ensuring product quality and reducing defects. The role of cleanrooms, equipped with advanced air filtration and circulation systems, is critical in this process. Choosing the right cleanliness class, optimizing air flow, and integrating efficient HVAC systems and sensors are all essential steps in constructing an effective cleanroom. Additionally, incorporating energy-efficient technologies and flexible design elements can further enhance the sustainability and adaptability of cleanrooms. One notable solution for optimizing cleanroom environments in semiconductor factories is the Huiya Raised Floor System for Semiconductor Cleanroom , which offers superior flexibility and efficiency in managing air distribution and cabling infrastructure. This system not only supports the stringent cleanliness requirements but also contributes to the overall energy efficiency and operational effectiveness of the cleanroom environment.