Anti-static raised access floors, also known as static dissipative floors or ESD flooring, are an essential component of modern computer rooms and other environments where electrostatic discharge (ESD) protection is required. These floors are designed to dissipate static electricity and prevent damage to sensitive electronic equipment. We will explore the various aspects of anti-static raised access floors, including their materials, specifications, ESD standards, applications, installation, and more.
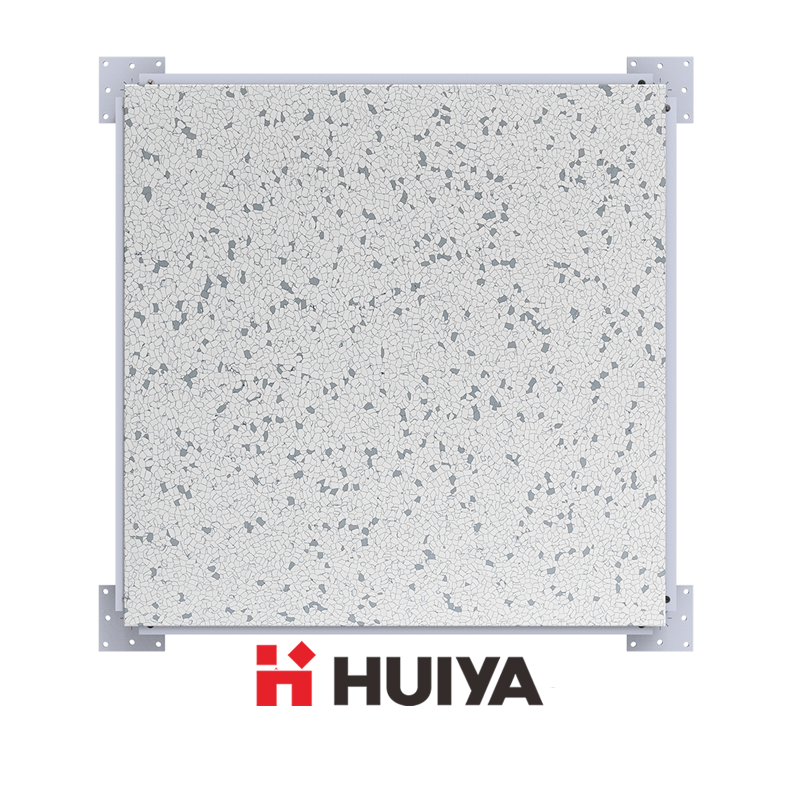
What is an Anti-Static Raised Access Floor?
An anti-static raised access floor, also known as a conductive raised floor, is a type of modular flooring system that is designed to dissipate static electricity. It consists of floor panels that are elevated above the actual floor on special pedestals, leaving an interstitial space below for utilities like cabling, cooling ducts, and piping.
The key characteristic of an anti-static raised floor is that its panels and structures have controlled conductivity – they are able to readily conduct away any static charge, preventing accumulation and potential damage from electrostatic discharge (ESD). This makes them perfect for use in spaces with electronic equipment that can be impacted by static electricity, such as data centers, cleanrooms, medical device manufacturing facilities, and server rooms.
Anti-Static Raised Access Floor Materials
There are a variety of materials used in the construction of anti-static raised floor panels and support structures:
- High-Pressure Laminate (HPL): HPL is a popular choice for the top covering of anti-static raised access floors. It is highly resistant to abrasion and offers excellent anti-static properties.
- Ceramic: Ceramic panels are another option for anti-static raised access floors. They provide superior durability and anti-static performance, making them suitable for high-traffic areas.
- Calcium Sulphate and Woodcore: Both materials are known for their excellent acoustic and anti-vibration properties. They are typically used in areas requiring noise control and stability.
- Steel: Steel panels are commonly used in anti-static raised access floors. They offer excellent load-bearing capacity and can withstand heavy equipment.
- Aluminum: Aluminum panels are lightweight and corrosion-resistant, making them suitable for environments with specific requirements.
- HPL and PVC: High Pressure Laminate (HPL) and Polyvinyl Chloride (PVC) are often used as the top finish due to their anti-static properties. They also provide a clean and aesthetic look.
For floor covering options, dissipative/conductive finishes include rubber, conductive vinyl flooring, ESD carpet tile, linoleum and laminate designed for static control applications. Proper grounding is also critical.
Anti-Static Raised Floor Specification
Regulatory standards outline the specifications for anti-static raised floors, including:
- Panel Size: The standard panel size for anti-static raised access floors is 600mm x 600mm. However, other sizes are also available to meet specific project requirements
Panel Thickness: The panel thickness typically ranges from 32mm to 40mm, depending on the material and load-bearing capacity. - Load-Bearing Capacity: Anti-static raised access floors are designed to support various loads, ranging from light office equipment to heavy machinery. The load-bearing capacity is specified in terms of ultimate load and rolling load.
- Fire Resistance: The materials used should have a high fire resistance rating to ensure safety.
- Surface Finish: The top covering of anti-static raised access floors can have different surface finishes, including HPL, PVC, rubber, steel plate, ceramic tile, or carpet.
Key specifications also cover tile sizes (600x600mm being standard), load ratings, finish and material durability, grounding/bonding, and cleanability for controlled environments. Proper installation methods help attain the specified conductivity levels.
ESD Standards for Anti-Static Raised Floors
Most modern facilities involving electronic equipment need to comply with Electrostatic Discharge (ESD) standards for flooring and work areas. Common standards for anti-static raised floors include:
- ANSI/ESD S20.20 (for floor surface resistance) – It should not exceed 1×10^9 ohms or be below 1×10^6 ohms.
- IEC 61340-5-1 Electrostatics – Part 5-1: Protection of electronic devices from electrostatic phenomena – General requirements.
- ESD TR53 Grounding – addresses grounding of raised floor systems to the building ground grid.
- EOS/ESD S8.1 Floor Materials and Coverings – Specifies low-resistivity flooring.
- EOS/ESD Association S6.1 (for floor materials) – Specifies low resistivity and non-accumulative characteristics.
- NFPA 75 Standard for the Protection of Electronic Computer/Data Processing Equipment.
- EN 61340-5-1 Electrostatics (for flooring in electrical rooms) – Protection of electronic devices from electrostatic phenomena – General requirements.
Properly specified and installed anti-static floors that comply with these standards provide the necessary protection.
Why Install Anti-Static Raised Floors?
There are several benefits of using an anti-static raised floor system rather than a conventional floor in applications prone to static discharge issues:
- Prevent ESD Damage: Static discharges that exceed equipment tolerances can damage electronics or disrupt operations. Anti-static floors eliminate this risk.
- Safer Equipment Handling: Staff can safely roll or move equipment without fear of damaging it through uncontrolled static buildup.
- System Uptime: Critical systems have fewer reboots or malfunctions due to ESD events, improving overall availability.
- Lower Maintenance: Replacing damaged components costs more than regular cleaning/replacement of anti-static flooring.
- Accessible Cable Management: Utilities laid below the floor simplify moves/changes and cable routing versus embedded systems.
- Flexible Spaces: Raised floors allow last-minute configuration changes without complicated floor work.
- Cooling Efficiencies: Under-floor airflow system optimization is possible with suspended floor plenums.
Where to Install Anti-Static Raised Floors?
Key environments where anti-static raised floors prove indispensable include:
- Data Centers – To safeguard servers and networking equipment from electrostatic damage.
- Cleanrooms – Cleanrooms, particularly in the semiconductor and pharmaceutical industries, utilize anti-static raised access floors to maintain a static-free environment and protect delicate processes.
- Laboratories – Laboratories dealing with sensitive electronic equipment or research require anti-static raised access floors to maintain a controlled environment and prevent ESD events.
- Server Rooms – For maintain uptime of business-critical IT infrastructure without downtime.
- Laboratories – To protect sensitive electronic test/measuring equipment in research facilities.
- Airport Control Towers – To prevent disruption of air traffic control systems from static.
- Call Centers – For uninterrupted operation of mission-critical contact centers.
- Office Spaces – Anti-static raised access floors can be installed in office spaces to provide cable management solutions and facilitate easy access to electrical and data connections
- Co-location Facilities – In internet housing facilities with dense rack deployments.
- Military Applications – For defense and aerospace electronic applications needing full ESD protection.
- Control Rooms – Control rooms, such as those in power plants or manufacturing facilities, often require anti-static raised access floors to ensure the reliable operation of critical systems
Proper Grounding is also necessary in all of the above settings for complete static control.
What to Consider Before Installing Anti-Static Floors?
When planning for an anti-static raised floor installation, it is important to carefully consider these factors:
- Standard Compliance – Confirm floor meets regulatory standards like ANSI/ESD S20.20 for your application.
- Tile Size & Openings – Standard 600x600mm tiles may not suit tight spaces; confirm compatibility.
- Load Requirements – Determine the load requirements based on the equipment and furniture that will be placed on the raised access floor.
- ESD Control – Assess the ESD sensitivity of the equipment and select the appropriate anti-static raised access
- Pedestal Type – Specify electromagnetic interference (EMI) grounded/non-grounded type as needed.
- Floor Covering Options – Choose optimal tile/surface material for application and aesthetics.
- Grounding Method – Decide on established grounding/bonding approach for complete system.
- Budget – Anti-static floors cost more initially but save on repairs; factor life cycle costs.
- Installation Disruptions – Plan downtime required and schedule appropriately.
- Cable Management – Provide for feeds below without overcrowding or cable damage risks.
Addressing these planning considerations leads to trouble-free raised floor installations.
How to Install Anti-Static Raised Floors?
Proper installation methods are vital in attaining the anti-static performance from raised access floors. The basic steps include:
- Surface Preparation: Ensure concrete slab is smooth, dry and any existing finishes removed. Apply conductive paint primer.
- Pedestal Layout: Mark layout and fasten pedestals securely using fixation plates or anchors at recommended spacing.
- Running Stringers: Join pedestals horizontally using grounded aluminum or stainless-steel stringers for structural support.
- Applying Grounding Materials: Lay conductive underlayment ensuring full contact. Bond floor to building ground system.
- Installing Tiles: Position tiles on pedestals, check for levelness and bond edges using conductive adhesive if required.
- Covering Application: Apply anti-static finish like conductive vinyl, carpet, rubber securely with adhesive.
- Electrical Testing: Verify floor resistance is within ESD standards using a megohmmeter before use.
- Periodic Testing: Repeat testing periodically and after repairs to confirm floor maintains conductivity.
Adhering to manufacturers’ instructions yields floors satisfying ESD specifications for safe operation. Proper maintenance also sustains the flooring’s anti-static properties long-term.
In conclusion, anti-static raised access floors provide the best risk-mitigation against static electricity dangers for sensitive electronics applications. When specified, installed and maintained according to established standards, they safely eliminate the threat of ESD damage to mission-critical systems and components.